「本当にその日に必要なものしか作らない」というポリシーのもと、タクトタイムを可視化。
個別製品の納期と生産工数を勘案し、最も効率的な生産計画を立案します。
加工を行う日に必要な部品がモレなく揃うようにコントロールすることで、歩留まり・設備稼働率向上、製品リードタイムの短縮を図り、最適なQ・C・Dの実現を目指しています。
Process1 – 受注
正和製作所はお客様のご希望納期をできる限り実現するよう努めております。お見積の時点で弊社からご呈示差し上げた納期は100%遵守。製造工程とスケジュールの管理を全社一丸となって徹底しています。また、EDI発注についてはお客様からお送りいただく発注データをすみやかに処理し、自社生産管理システムとのインターフェイスをスムーズに取れるシステムを独自開発。情報の一元化によるスピーディーかつ確実なオペレーションで、お客様の様々なニーズにお応えいたします。
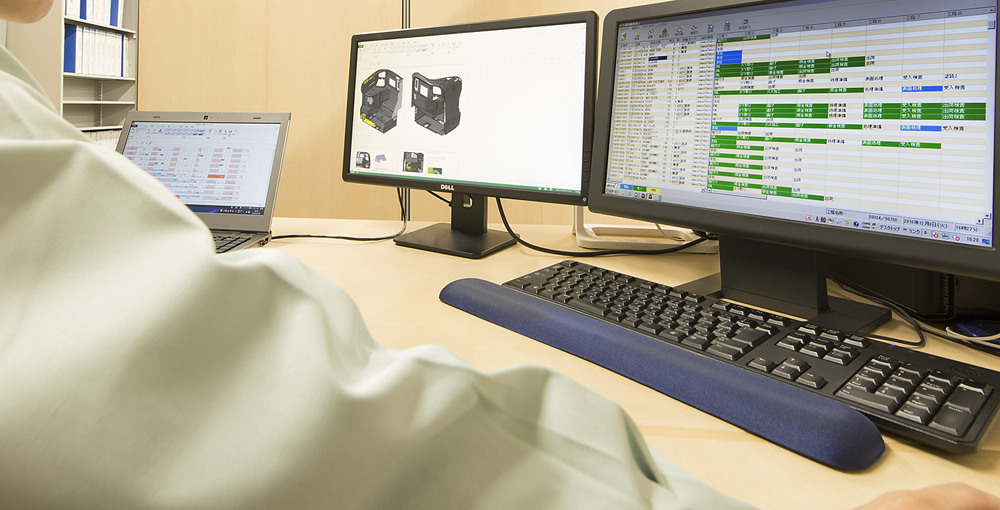
- 購買管理業務
- 客先受発注業務
- 社内手配業務
- 購入資材購買業務
- 製造後各種処理発注受入業務
- 受入検査及び出荷検査業務
- 出荷業務

Process2 – 設計
3次元板金設計のメリットはCAMとシームレスに連係し、延びがどれくらいになるかの展開長が導き出せること。3次元で設計し、それを2次元化して一枚の板へ展開することで加工精度が飛躍的に向上します。現在では一般化しつつありますが、3次元CAD/CAMのメリットを最大限に引き出すため、設計したプログラムのデータを製造工程まで連係して利用できる仕組みを日本で初めて取り入れました。CAD機能はベースCADに効率的な生産設計を可能にするSolidWorksを採用しております。
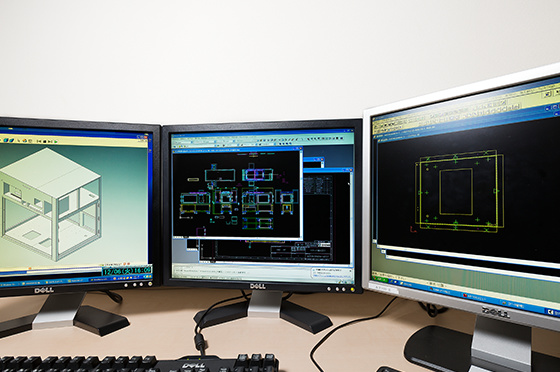
●3次元ソリッド 板金CAD システム
●CAD 機能
●データインポート

Process3 – 製造
一枚の原料板上に複数種の部品を割り付けるネスティングを徹底的に追求した結果、「本当にその日に必要なものしか作らない」というポリシーが生まれました。タクトタイムが可視化できるため、個別の製品の納期と生産数を勘案しながら最も効率的な生産計画を組めるようになっています。加工を行う日に必要な部品がモレなく揃うようにコントロールすることで、歩留まりと設備稼働率、そして製品リードタイムの最適化を図ることが可能になりました。
●ASIS100PCL
●自動プロ(AP100)
●NC 装置
●デーリーネスティング
●製品リードタイムの向上
●歩留まり率
●設備稼働率
●国家資格保有者
●溶接技能者
●溶接作業指導者

Process4 – ニ次処理
仕上げを左右するのはやはり熟達した職人の技量。腕の良い技術者が詰まりしろを読みながら溶接したものでも、微妙な調整は欠かせません。研磨や表面処理、塗装、印刷なども同様です。弊社ではレベルの高い二次処理を行えるよう、外部協力会社とも常に情報交換を行いながら作業を進めております。特に塗装と鍍金(化成被膜・陽極酸化被膜含む)におきましては色差計と膜圧計を用いて管理することで確実な品質保証体制を展開しております。
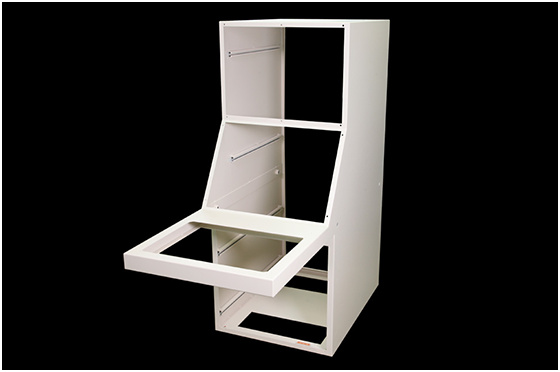
●色差計
●膜厚計

Process5 – 検査
精度の高い工作機械で製造し、熟練した技術者が組み上げた製品。品質が盤石であると思われればこそ、検査のプロセスが重要となります。万が一の可能性をゼロにすると同時に造り込み品質のさらなる向上を図るため、高精度の測定機器を用いたチェックを重ね
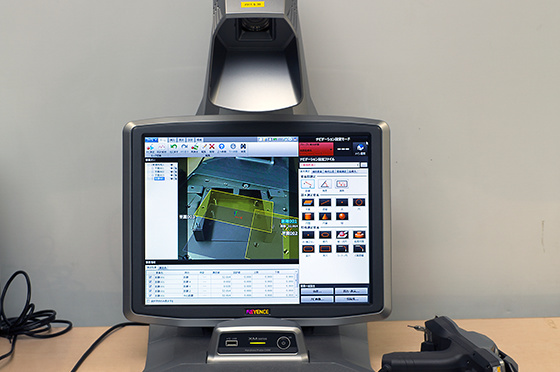
●測定機器
●造り込み品質

Process6 – アッセンブリ
高度成長期に通信機や産業機器系の板金製品製造を皮切りに、板金で作る金属の部品類をユニットへ収めるサブアッセンブリを手がけるようになり、長きにわたって加工技術を培って参りました。大小様々な大きさの筐体へ電気配線を組み込むアッセンブリ加工もおまかせください。
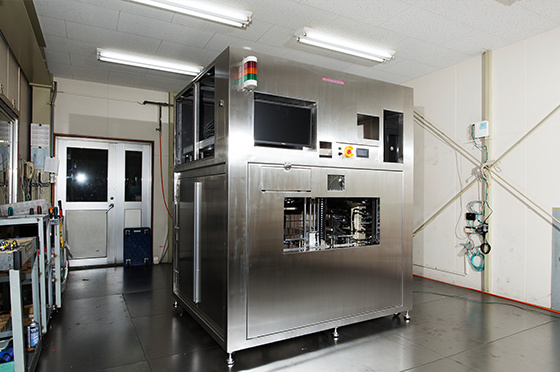
●筐体
●アッセンブリ加工

Process7 – 出荷(出荷検査含む)
完成した製品は責任を持ってご指定の場所まで大切にお届けいたします。設置場所や搬入経路に制約があり、製品を分割して納品できるようにというご要望などにもきめ細かく対応させていただきます。どうぞお気軽にご相談ください。